Piezo Actuators for the Dynamic and Precise Clocking of the Nozzle Shutter
Piezo Actuators for the Dynamic and Precise Clocking of the Nozzle Shutter
The variety of materials and applications in plastics processing is increasing continuously. This trend was recognized early on by the machine engineering specialists Arburg who, in addition to the classical injection molding for this growing market, have developed another industrial process: The Arburg Plastic Freeforming (APF) is a so-called freeformer that allows a large amount of design freedom and material diversity and also realizes part geometries that normally could not be formed using injection molding.
Functional Principle
The central process of additive manufacturing is the generation of the droplets at the nozzle of the discharge unit. Piezo actuators convert electrical energy directly into mechanical energy and enable motion with subnanometer resolution. They achieve travel ranges up to approximately one millimeter and high dynamics with frequencies up to several thousand Hertz. The discharge unit on the freeformer currently works with frequencies between 60 and 200 Hz.
- Basic requirement: Qualified standard granulate
- Material treatment with screw in the same way as injection molding
- Material reservoir between the screw and nozzle tip is under pressure
- Piezo actuator clocks the nozzle shutter
- Nozzle shutter
- Discharge of individual drops at the nozzle tip
- Component holder moves the component in the X and Y direction as well as the stepwise downwards in the Z direction
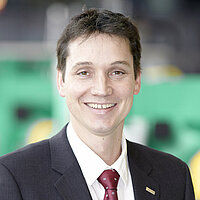
For generating the droplets, we decided to use a piezo actuator for clocking the nozzle shutter because this provides the necessary high dynamics and accuracy for the material discharge.
Properties of the Piezo Actuator
In addition to accuracy and dynamics, the PICMA® actuator that is used for clocking the nozzle shutter during the APF process, has a number of other features that predestine it for use in industrial additive manufacturing. The actuator designed to customer specifications has travel ranges up to 90 µm with subnanometer resolution, can be pressure-loaded to 3,000 N and its microsecond response time makes it exceptionally fast. No other valve technology offers such a fast response time at a comparable size.
Furthermore, PICMA® actuators surpass conventional, polymer-coated piezo actuators in performance and lifetime because of their all-ceramic insulation. The ceramic insulation layer protects the monolithic piezoceramic block against humidity, and failure due to increased leakage current, and therefore achieves high motion cycles under extreme ambient conditions. The monolithic structure also causes a high resonant frequency, which is the reason why these actuators are ideally suited to highly dynamic applications.
Do you have questions about our solutions? Our specialists are happy to help you!
Contact us today!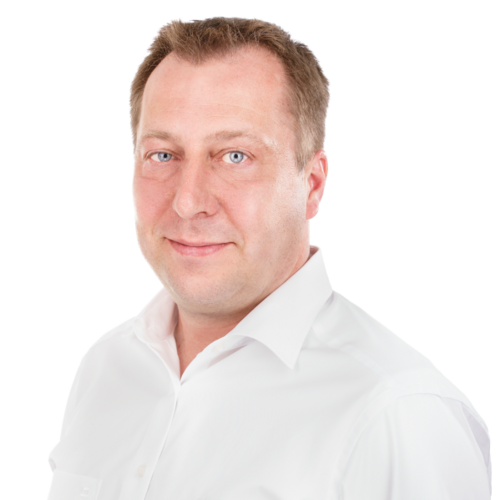