High-Performance Motion and Control Solutions for Improving Throughput and Precision in Laser Materials Processing
The first laser beam was generated in 1960 with a ruby laser – today, about 60 years later – they are indispensable tools in industrial materials processing. In ablation, cutting, micromachining, drilling, or welding – in a great variety of procedures, they optimize manufacturing processes and make many future technologies even possible. For example, the electronics sector and the automotive or semiconductor industries benefit from the advanced capabilities of laser material processing.
However, process, material, work cycle, ambient conditions, and criteria such as throughput, precision, geometry, and size of the machining surface make very different demands on machine builders, system integrators, and also on the basic components of any system: The positioning of the workpiece, the laser, and their motion control. But the one and only system does not exist since solutions are as individual as there are different applications.
In order to develop the appropriate positioning solution that can also be optimally integrated into the application, PI works closely with its customers right from the start. Due to the variety of technologies and experience in precision positioning and automation, PI can react flexibly to the requirements of laser technology and offer motion solutions that meet customer needs: From single and multi-axis systems without beam deflection to highly customized solutions where the motion of galvanometer scanners and the positioning systems have to be synchronized and are able to run simultaneously.
ACS Motion Control, as part of the PI Group, allows the supply of highly sophisticated automation and motion controllers with a wide range of drive options and dedicated modules for the control of laser applications.
Automation Platforms for Laser Material Processing
Precision – Throughput – Synchronized Motion
Do you have questions about our solutions? Our specialists are happy to help you!
Contact us today!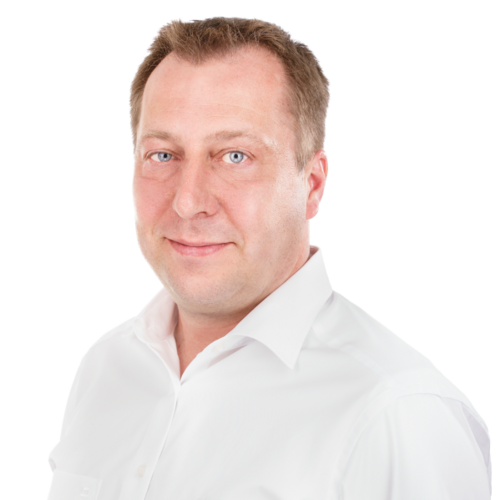