Precision hexapod; brushless DC gear motor; absolute encoder; 50 kg payload; 8 mm/s maximum velocity. Connecting cables are not included in the scope of delivery and must be ordered separately.
H-850 Hexapod
For Loads to 250 kg
- Repeatability to ±0.2 µm
- Travel range ±50 mm / ±50 mm / ±25 mm
- Rotation range ±15° / ±15° / ±30°
- Minimum incremental motion to 0.3 µm / 0.3 µm / 0.25 µm
- Absolute encoder









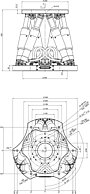
The H-850 series hexapods position loads of up to 250 kg with high precision and reliability. Heavy-duty precision bearings allow applications with long duty cycles.
The parallel-kinematic design for 6 degrees of freedom makes it significantly more compact and stiffer than comparable serial kinematic systems. The advantages over serial, i.e., stacked systems, are mainly the much better path accuracy and repeatability. In addition, the moved mass is lower and allows improved dynamics which is the same for all motion axes. Cable management is not a problem because cables are not moved.
Use of BLDC motors
Brushless DC motors are particularly suitable for high rotational speeds. They can be controlled very accurately and ensure high precision. Because they dispense with sliding contacts, they run smoothly, are wear-free and therefore achieve a long lifetime.
Absolute encoder
Absolute encoders supply explicit position information that enables immediate determination of the position. Therefore, no referencing is necessary when switching on and this increases efficiency and safety during operation.
PIVirtualMove
The simulation software simulates the limits of the workspace and payload of a hexapod. Therefore, even before purchasing, you can check whether a particular hexapod model can handle the loads, forces, and torques occurring in an application. For this purpose, the simulation tool takes the position and motion of the hexapod as well as the pivot point and several reference coordinate systems into account.
Application fields
Industry and research. For astronomy, optics positioning, aerospace.
Specifications
Specifications
Motion | H-850.G2A | H-850.H2A | Tolerance |
---|---|---|---|
Active axes | X ǀ Y ǀ Z ǀ θX ǀ θY ǀ θZ | X ǀ Y ǀ Z ǀ θX ǀ θY ǀ θZ | |
Travel range in X | ± 50 mm | ± 50 mm | |
Travel range in Y | ± 50 mm | ± 50 mm | |
Travel range in Z | ± 25 mm | ± 25 mm | |
Rotation range in θX | ± 15 ° | ± 15 ° | |
Rotation range in θY | ± 15 ° | ± 15 ° | |
Rotation range in θZ | ± 30 ° | ± 30 ° | |
Maximum velocity in X | 8 mm/s | 0.5 mm/s | |
Recommended velocity in X | 5 mm/s | 0.3 mm/s | |
Maximum velocity in Y | 8 mm/s | 0.5 mm/s | |
Recommended velocity in Y | 5 mm/s | 0.3 mm/s | |
Maximum velocity in Z | 8 mm/s | 0.5 mm/s | |
Recommended velocity in Z | 5 mm/s | 0.3 mm/s | |
Maximum angular velocity in θX | 120 mrad/s | 6 mrad/s | |
Recommended angular velocity in θX | 75 mrad/s | 3 mrad/s | |
Maximum angular velocity in θY | 120 mrad/s | 6 mrad/s | |
Recommended angular velocity in θY | 75 mrad/s | 3 mrad/s | |
Maximum angular velocity in θZ | 120 mrad/s | 6 mrad/s | |
Recommended angular velocity in θZ | 75 mrad/s | 3 mrad/s | |
Positioning | H-850.G2A | H-850.H2A | Tolerance |
Minimum incremental motion in X | 1 µm | 0.3 µm | typ. |
Minimum incremental motion in Y | 1 µm | 0.3 µm | typ. |
Minimum incremental motion in Z | 0.5 µm | 0.2 µm | typ. |
Minimum incremental motion in θX | 7.5 µrad | 3 µrad | typ. |
Minimum incremental motion in θY | 7.5 µrad | 3 µrad | typ. |
Minimum incremental motion in θZ | 15 µrad | 5 µrad | typ. |
Unidirectional repeatability in X | ± 0.5 µm | ± 0.6 µm | typ. |
Unidirectional repeatability in Y | ± 0.5 µm | ± 0.6 µm | typ. |
Unidirectional repeatability in Z | ± 0.2 µm | ± 0.2 µm | typ. |
Unidirectional repeatability in θX | ± 3 µrad | ± 3 µrad | typ. |
Unidirectional repeatability in θY | ± 3 µrad | ± 3 µrad | typ. |
Unidirectional repeatability in θZ | ± 7.5 µrad | ± 9 µrad | typ. |
Backlash in X | 6 µm | 4 µm | typ. |
Backlash in Y | 6 µm | 4 µm | typ. |
Backlash in Z | 1.5 µm | 0.5 µm | typ. |
Backlash in θX | 25 µrad | 7.5 µrad | typ. |
Backlash in θY | 25 µrad | 7.5 µrad | typ. |
Backlash in θZ | 90 µrad | 60 µrad | typ. |
Integrated sensor | Absolute rotary encoder, multi-turn | Absolute rotary encoder, multi-turn | |
Drive Properties | H-850.G2A | H-850.H2A | Tolerance |
Drive type | Brushless DC gear motor | Brushless DC gear motor | |
Mechanical Properties | H-850.G2A | H-850.H2A | Tolerance |
Stiffness in X | 7 N/µm | 7 N/µm | |
Stiffness in Y | 7 N/µm | 7 N/µm | |
Stiffness in Z | 100 N/µm | 100 N/µm | |
Maximum load capacity, base plate in any orientation | 20 kg | 50 kg | |
Maximum load capacity, base plate horizontal | 50 kg | 250 kg | |
Maximum holding force, base plate in any orientation | 85 N | 500 N | |
Maximum holding force, base plate horizontal | 250 N | 2000 N | |
Overall mass | 17 kg | 17 kg | |
Material | Aluminum | Aluminum | |
Miscellaneous | H-850.G2A | H-850.H2A | Tolerance |
Operating temperature range | -10 to 50 °C | -10 to 50 °C | |
Connector for data transmission | HD D-sub 78 (m) | HD D-sub 78 (m) | |
Connector for supply voltage | M12 4-pole (m) | M12 4-pole (m) | |
Recommended controllers/drivers | C-887.5xx | C-887.5xx |
Connecting cables are not included in the scope of delivery and must be ordered separately.
Ask about customized versions.
When measuring position specifications, typical velocity is used. The data is included in the delivery of the product in the form of a measurement report and is stored at PI.
The maximum travel ranges of the individual coordinates (X, Y, Z, θX, θY, θZ) are interdependent. The data for each axis shows its maximum travel range when all other axes are in the zero position of the nominal travel range and the default coordinate system is in use, or rather when the pivot point is set to 0,0,0.
At PI, technical data is specified at 22 ±3 °C. Unless otherwise stated, the values are for unloaded conditions. Some properties are interdependent. The designation "typ." indicates a statistical average for a property; it does not indicate a guaranteed value for every product supplied. During the final inspection of a product, only selected properties are analyzed, not all. Please note that some product characteristics may deteriorate with increasing operating time.
Downloads
Product Note
Product Change Notification Motor Driven Products
Product Change Notification H-850.H2, H-850.G2
Product Change Notification Hexapod Cables
Product Change Notification H-206.x1x, H-8xx.x1x, H-8xx.xVx, F-206.S
Datasheet
Documentation
User Manual MS202
H-850 Hexapod Microrobot with Excellent Position Repeatability
3D Models
3-D model H-850.x2x
Software Files
PIVirtualMove
Ask for a free quote on quantities required, prices, and lead times or describe your desired modification.
Precision hexapod; brushless DC gear motor; absolute encoder; 250 kg payload; 0.5 mm/s maximum velocity. Connecting cables are not included in the scope of delivery and must be ordered separately.
How to Get a Quote
Ask an engineer!
Quickly receive an answer to your question by email or phone from a local PI sales engineer.
Technology
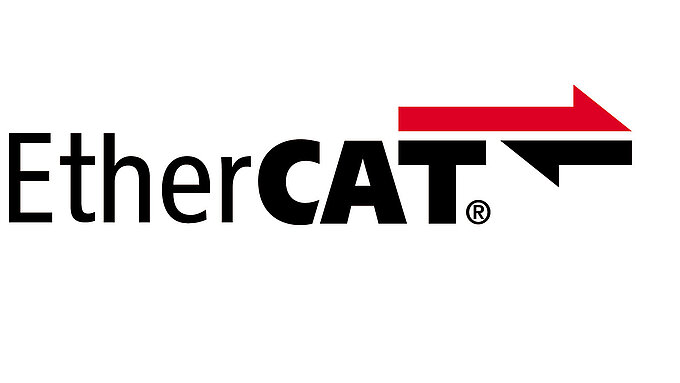
EtherCAT Connectivity of PI Products
PI offers high-precision drives for use as EtherCAT slave, or integrates with ACS Motion Controllers as Master, or 2nd Master in an existing architecture.
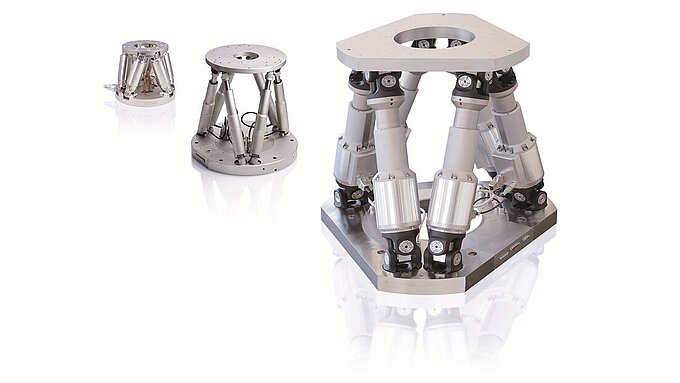
Hexapods and SpaceFAB
Hexapods are systems for moving and positioning loads in six degrees of freedom, in three translational and three rotational axes.
Applications
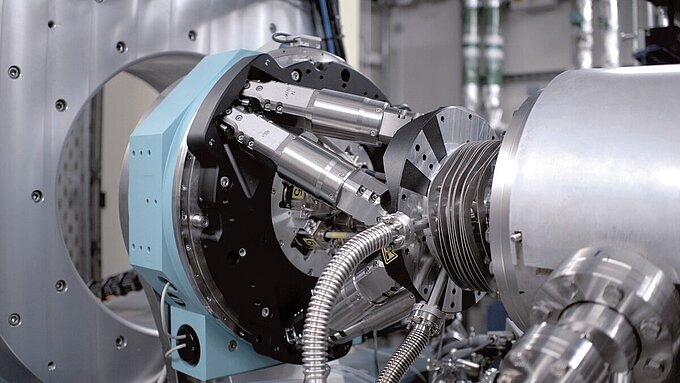
Sample Adjustment
At Diamond Light Source, UK, beamline I07 is a high-resolution X-ray diffraction beamline dedicated to investigate the structure of surfaces and interfaces.
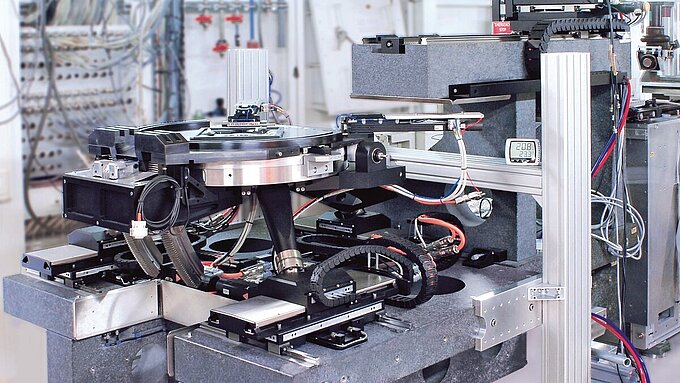
Positioning for Laminography
High-Precision Spatial Positioning of Flat, Extended Objects
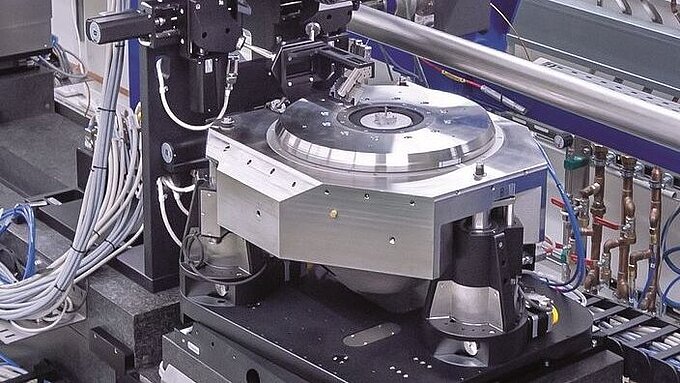
Nanotomography
At the X-ray light source PETRA III at the DESY research center in Hamburg operates the Imaging Beamline P05.
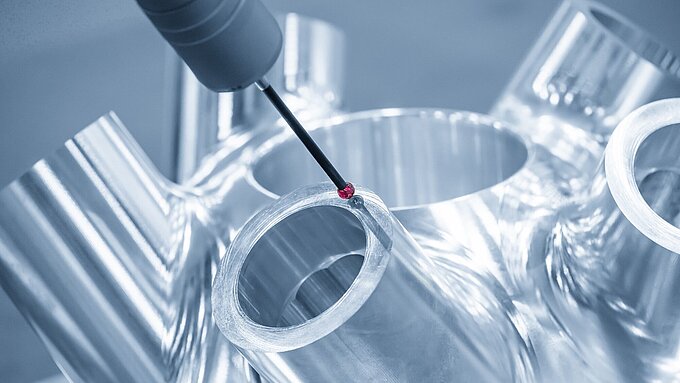
Dimensional Measuring
Hexapods allow for an outstanding flexibility for a variety of samples of in-line automation systems by minimizing the space for motion robotics.